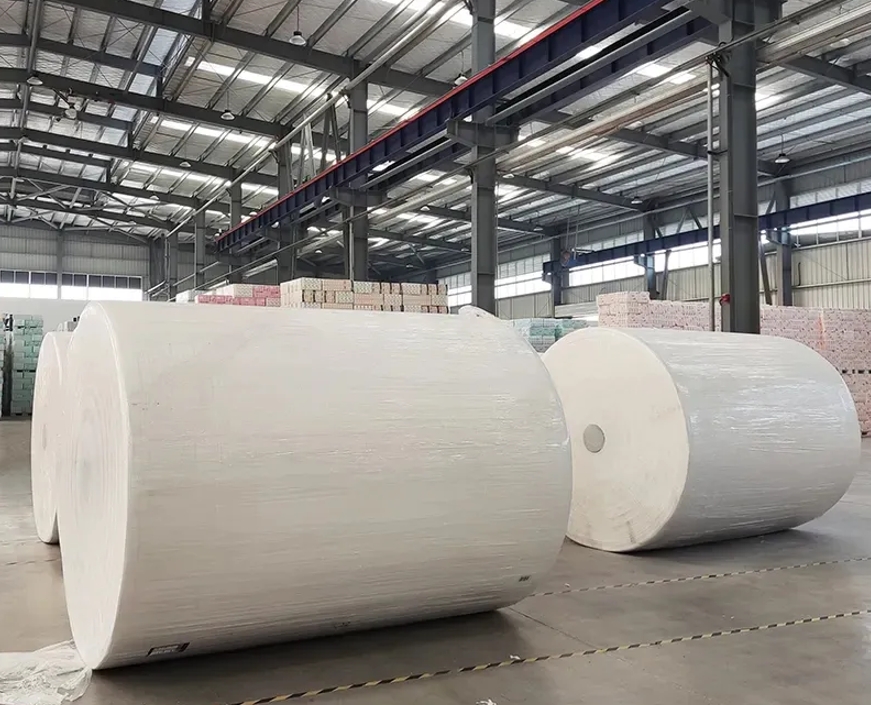
In the tissue production industry, converting plays a crucial role. It transforms large parent rolls into consumer-ready tissue products. This process ensures that you receive high-quality tissue products that meet your daily needs. The production process of parent roll/mother roll that used for converting tissue paper involves several steps. These steps ensure the quality and consistency of the final product. With the global tissue paper market projected to grow from USD 82 billion in 2022 to around USD 135.51 billion by 2030, understanding this conversion process becomes even more significant.
Production Process of Parent Roll/Mother Roll Used for Converting Tissue Paper
Material Requirements and Quality Control
When you delve into the production process of Mother Roll Reel that used for converting tissue paper, understanding the material requirements becomes essential. Tissue Parent Rolls primarily come in two types: virgin wood pulp and recycled paper. Virgin wood pulp, known for its softness and strength, is mechanically separated and refined from wood fibers. This type is often preferred for products like Facial Tissue Parent Rolls, where quality and performance are paramount. On the other hand, recycled paper undergoes deinking and pulping, offering an eco-friendly alternative.
Quality control plays a pivotal role in ensuring that the parent rolls meet the necessary standards. You must consider factors such as customer preferences, production costs, and environmental regulations. By maintaining stringent quality checks, you ensure that the final tissue products are consistent and reliable.
Production Steps of Parent Tissue Jumbo Roll
The production process of Best Jumbo Mother Roll that used for converting tissue paper involves several key steps:
1.Pulp Preparation: You start by preparing the pulp, which involves breaking down the raw materials into a fibrous slurry. This step is crucial for both virgin and recycled materials.
2.Sheet Formation: The pulp is then spread onto a moving screen to form a continuous sheet. Water is removed, and the sheet begins to take shape.
3.Pressing and Drying: You press the sheet to remove excess water and then dry it using heated rollers. This step ensures the sheet's strength and durability.
4.Winding into Jumbo Rolls: Finally, the dried sheet is wound into large rolls, known as Toilet Tissue Parent Roll or jumbo rolls. These rolls serve as the foundation for producing smaller consumer-sized products.
Throughout these steps, you must conduct regular inspections to maintain quality. By doing so, you ensure that the parent rolls are ready for the next stage of converting into tissue products.
Overview of the Converting Process
The conversion of Parent Roll Base Paper into consumer-ready tissue products involves several key stages. Each stage plays a vital role in ensuring the quality and usability of the final product.
Initial Preparation
Unwinding Parent Rolls
When begin the converting process by unwinding the large parent rolls. This step is crucial as it prepares the rolls for further processing. The unwinding process ensures that the tissue paper is free from tension, which can affect the quality of the final product. By carefully controlling the unwinding speed, you maintain the integrity of the tissue paper.
Inspection and Quality Control
Once the parent rolls are unwound, you must conduct a thorough inspection. Quality control measures are essential at this stage to identify any defects or inconsistencies in the tissue paper. You ensure that only the highest quality rolls proceed to the next stage. This attention to detail guarantees that the final products meet consumer expectations.
Cutting and Rewinding
Slitting Machines
After inspection, you use slitting machines to cut the tissue paper into smaller, manageable sizes. These machines are designed to handle the delicate nature of tissue paper, ensuring clean and precise cuts. By using advanced slitting technology, you achieve consistent results that enhance the overall quality of the tissue products.
Rewinding Techniques
Once the tissue paper is cut, you employ rewinding techniques to roll the paper onto smaller cores. This step is crucial for creating consumer-sized products. By carefully controlling the tension during rewinding, you prevent issues such as wrinkling or tearing. This ensures that the tissue products are ready for packaging and distribution.
Embossing and Perforatin
Embossing Patterns
Embossing adds texture and design to the tissue paper, enhancing its aesthetic appeal and functionality. You can choose from a variety of embossing patterns to create unique and attractive products. This step not only improves the appearance of the tissue paper but also increases its absorbency and softness.
Perforation for Easy Tearing
Perforation is the final step in the converting process. By adding perforations, you make it easy for consumers to tear the tissue paper into desired lengths. This feature is especially important for products like toilet paper and paper towels. By ensuring precise perforations, you enhance the convenience and usability of the tissue products.
The production process of 100% Virgin Parent Roll that used for converting tissue paper is a complex yet fascinating journey. Each step, from unwinding to perforating, contributes to the creation of high-quality tissue products that meet consumer needs.
Machinery and Operations
Key Machinery Used
Slitters and Rewinders
In the tissue converting process, slitters play a vital role. They cut large parent rolls into smaller, more manageable sizes. You use these machines to ensure precise cuts, which are essential for maintaining the quality of the tissue products. The rewinders then take over, rolling the cut tissue onto smaller cores. This step is crucial for creating consumer-sized products. By using advanced rewinding techniques, you prevent issues like wrinkling or tearing, ensuring that the tissue products are ready for packaging and distribution.
Embossers and Perforators
Embossers add texture and design to the tissue paper, enhancing its aesthetic appeal and functionality. You can choose from a variety of embossing patterns to create unique and attractive products. This step not only improves the appearance of the tissue paper but also increases its absorbency and softness. Perforators are used to add perforations, making it easy for consumers to tear the tissue paper into desired lengths. This feature is especially important for products like toilet paper and paper towels. By ensuring precise perforations, you enhance the convenience and usability of the tissue products.
Automation and Technology
Role of Automation in Efficiency
Automation plays a significant role in the efficiency of tissue converting operations. By implementing automated systems, you can achieve higher throughput and reduce downtime. The continuous nature of roll-to-roll manufacturing allows for uninterrupted production, improving outcomes and accuracy. Automated systems maintain proper paper tension throughout the machine, ensuring consistent quality. The use of automation reduces mechanical components, leading to less downtime and increased design flexibility.
Technological Advancements
Technological advancements have revolutionized the tissue converting industry. State-of-the-art tissue converting plants, like those developed by MAFLEX, focus on software monitoring, efficiency, and safety. These plants implement various devices and measures to enhance production efficiency and workplace safety. The HERACLE embossing roll system allows for fully automatic roll changes, streamlining the production process. By embracing these technological advancements, you can ensure a smooth and effective converting process, resulting in high-quality tissue products that meet consumer needs.
Safety Considerations and Best Practices
Safety Protocols
Operator Training
You must prioritize operator training to ensure safety in tissue converting operations. Proper training equips operators with the knowledge and skills needed to handle machinery safely. You should focus on teaching them how to operate equipment, recognize potential hazards, and respond to emergencies. Regular training sessions help keep operators updated on the latest safety practices and technological advancements.
Equipment Maintenance
Maintaining equipment is crucial for safe and efficient operations. You should implement a routine maintenance schedule to inspect and service machinery regularly. This practice helps identify and address potential issues before they lead to accidents or downtime. By keeping equipment in optimal condition, you enhance safety and prolong the lifespan of your machinery.
Best Practices
Quality Assurance
Quality assurance plays a vital role in producing high-quality tissue products. You should establish strict quality control measures throughout the converting process. Regular inspections and testing ensure that the final products meet industry standards and consumer expectations. By maintaining high-quality standards, you build trust with your customers and enhance your brand reputation.
Environmental Considerations
Environmental considerations are essential in modern tissue production. You should adopt eco-friendly practices to minimize your environmental impact. Using recycled materials, reducing waste, and optimizing energy consumption are effective strategies. By prioritizing sustainability, you contribute to environmental conservation and appeal to environmentally conscious consumers.
Benefits of the Converting Process
The production process of Paper Parent Jumbo Roll that used for converting tissue paper offers numerous benefits. These advantages enhance both the quality and efficiency of the final tissue products, ensuring they meet consumer expectations.
Enhanced Product Quality
Consistency and Reliability
When you engage in the production process of mother roll that used for converting tissue paper, you ensure a high level of consistency and reliability in the final products. The converting process allows you to maintain uniformity across all tissue products. This consistency is crucial for building trust with consumers, as they expect the same quality with every purchase. By adhering to strict quality control measures, you can deliver reliable tissue products that meet industry standards.
Customization Options
The converting process also provides you with the flexibility to customize tissue products according to consumer preferences. You can choose from various embossing patterns, perforation styles, and sizes to create unique products that stand out in the market. This customization capability allows you to cater to diverse consumer needs, enhancing the appeal of your tissue products.
Increased Efficiency
Cost-Effectiveness
The production process of parent roll/mother roll that used for converting tissue paper is designed to be cost-effective. By optimizing the use of raw materials and minimizing waste, you can reduce production costs significantly. This cost-effectiveness translates into competitive pricing for consumers, making your tissue products more attractive in the market. Additionally, the use of advanced machinery and automation further enhances operational efficiency, contributing to overall cost savings.
Time-Saving Aspects
Efficiency in the converting process also means saving time. The streamlined production process of parent roll/mother roll that used for converting tissue paper allows you to produce large quantities of tissue products in a shorter time frame. Automated systems and advanced technology play a crucial role in speeding up production, ensuring that you can meet high demand without compromising on quality. This time-saving aspect is vital for maintaining a competitive edge in the fast-paced tissue industry.
In summary, the production process of Paper Napkin Jumbo Roll that used for converting tissue paper offers significant benefits. By focusing on enhanced product quality and increased efficiency, you can produce high-quality tissue products that satisfy consumer needs while maintaining cost-effectiveness and time efficiency.
You have explored the intricate process of converting parent rolls into high-quality tissue products. This journey involves key steps like unwinding, cutting, embossing, and perforating, all facilitated by advanced machinery such as slitters, rewinders, embossers, and perforators. Safety and best practices remain paramount, ensuring both operator well-being and product excellence. By understanding this process, you appreciate the benefits of enhanced product quality and increased efficiency. As you delve deeper into the tissue production industry, you uncover opportunities for innovation and improvement, contributing to a sustainable and consumer-focused future.
Post time: Nov-19-2024